FAQ on Automation of Occupational Safety and Health Processes
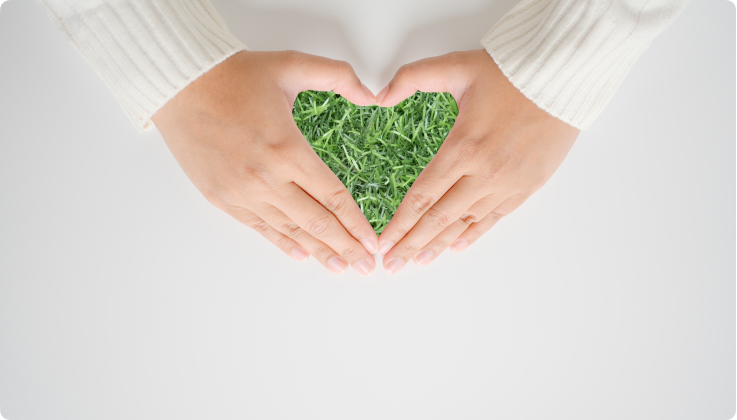
Why is automation of occupational safety and health processes important in manufacturing?
Automation of occupational safety and health (OSH) processes in manufacturing is a critical aspect of modern production management. It aims to reduce the risks of workplace injuries and illnesses while ensuring worker safety and health.
Automation enables the following:
- Improved management quality and efficiency: Automated processes provide accurate and timely monitoring of production, allowing for quicker responses to hazardous situations and their prevention.
- Enhanced worker safety and health: Automation ensures better control over workplace safety and improves the dissemination of safety and health information.
- Reduced costs for workplace injury compensation: By minimizing workplace accidents and illnesses, automation helps cut expenses associated with compensation payments.
- Compliance with legal requirements: Automation helps enterprises meet legal safety and health regulations, reducing the risk of fines and penalties.
In summary, automation of OSH processes is essential for improving workplace safety, enhancing production efficiency, and reducing injury and illness risks.
Which enterprises need OSH process automation?
OSH process automation is vital for all manufacturing facilities with hazardous working conditions or risks to worker health.
Examples include:
- Manufacturing plants using heavy machinery and equipment.
- Mining enterprises, where hazardous chemicals, gases, or potentially dangerous raw materials are handled.
- Construction companies involved in high-risk activities such as working at heights, confined spaces, or excavation, with risks of falling objects or heavy lifting operations.
- Energy companies, operating in environments with hazardous processes for generating, transmitting, or distributing electricity.
- Transportation companies dealing with hazardous goods or vehicles.
Regardless of the activity type, ensuring safe working conditions and preventing injuries and illnesses is critical. Therefore, OSH process automation is necessary wherever required.
How can OSH processes be automated in enterprises?
There are various ways to automate OSH processes in enterprises, such as:
- Using software for OSH management: These systems automate safety controls and management, track incidents, ensure equipment and material compliance, schedule and conduct inspections, issue work permits for hazardous jobs, track health records, and generate reports.
- Specialized safety equipment: For example, automatic fall protection systems or special ladders can be used in environments where falling from heights is a risk.
- Mobile safety apps: These apps provide workers with updated safety information, enable online training, and allow for safety checks to be marked as complete.
- Video surveillance systems: These detect safety violations, such as improper equipment use or unauthorized presence in restricted areas, enhancing workplace safety.
- Drones for inspections: Drones can inspect high or remote areas more efficiently and safely than manual inspections, reducing injury risks.
Each enterprise must analyze its specific risks and choose solutions suited to its unique requirements and production specifics.
Is there statistical evidence of reduced accidents and injuries after OSH automation?
Yes, numerous studies and reports confirm the positive impact of OSH automation on reducing accidents and injuries.
- A study by Aberdeen Group (“Safety in the Age of IIoT,” 2015) revealed a 10% decrease in workplace incidents in companies using specialized safety software compared to those without such systems.
- Research by Marsh Risk Consulting showed a 28% reduction in incidents and a 26% cut in compensation expenses in enterprises employing safety systems.
Automation significantly reduces workplace risks, especially in hazardous industries like mining and petrochemical production.
How is OSH automation software implemented?
Implementing OSH automation software typically involves several stages:
- Needs analysis: Assessing production processes, identifying threats, and determining software requirements.
- Software selection: Choosing software that aligns with enterprise safety standards and specific needs.
- Preparation for implementation: Training staff, preparing production data for automation, and ensuring compatibility with existing systems.
- Data preparation and integration: Gathering necessary information and integrating the system with existing tools, such as HR management software.
- Software implementation: Installing and configuring the software, conducting tests to ensure proper and safe operation.
- Employee training: Providing theoretical and practical training on using the software.
- Support and maintenance: Monitoring the software, resolving issues, and updating it as needed.
Effective implementation requires careful planning, preparation, and collaboration between the contractor and the client.